It's not unusual to see bubbles rising in a freshly applied epoxy coat. The most common cause of this is called “outgassing.” Outgassing is a natural process that occurs when trapped air or gasses from the concrete are released and creates blisters, craters, bubbles, or pinholes in epoxy floors.
Detecting Outgassing
Differentiating the types of breaks in your epoxy coating helps you to determine if outgassing has occurred. Two distinctive faults arise from outgassing. One is if you see small blisters, referred to as pinholes. After pinholes pop, they leave a small round crater in the coating; this is where the gas releases. The other sign of outgassing is any sized bubbles emerging out of the coating.
Causes of Outgassing
Outgassing that results in pinholes and craters is a result of residual silicone, oil, or grease that is left on the surface of the flooring before applying the epoxy. When applied on top of these residuals there is an increase in temperature, and the epoxy reacts with the residual oils and creates pinhole faults.
Outgassing can be caused by a change in the room’s temperature as the epoxy is curing, which is the process in which the epoxy is hardening. The change in a room’s temperature may result in bubbles forming in the layers of the epoxy. These bubbles continue to form, expand, and rise until they are released from the surface. In addition to temperature changes, an increase in humidity can prevent the epoxy to not set and can lead to bubbles or failure to bond due to trapped moisture.
Other causes of faults are contingent on the preparation of your epoxy products. One is engaging in a high powered mixing of the resin and hardener solutions which causes more bubbles to emerge. Using excessive solvent may produce an overflow of evaporation, which leaves pinholes in the surface of the epoxy. These causes can be avoided with a careful application of each epoxy product and by retaining a consistent temperature throughout the application process.
Fixing Outgassing Effects
Many minor fixes may fix the bubbles and pinholes in the epoxy, but the best way to fix and release excess gas and air that is trapped is applying another coat of epoxy. To do this, first, sand the epoxy using a rotary scrubber or a palm sander for small areas. For larger areas of bubble clusters, it may be easier to use a floor buffer. However, if there are bubbles in the entirety of your floor, use a diamond grinder or hand grinder which will remove the existing epoxy coating. Remember to use medium or hard blasting options to ensure your faulty epoxy coat is removed. Next, vacuum the dust and with a clean cloth, dip it in solvent solution and wipe your floor evenly. This step is very crucial because it removes dust and debris that may interfere with the bonding of your new epoxy, and the solvent helps the epoxy adhere to your floor evenly, which prevents bubbles from emerging. Finally, apply another coat of epoxy, but remain cognizant of the many causes of bubbles and pinholes in the epoxy to avoid a blemished coat.
There is no way to anticipate that the effects of outgassing will arise in a slab until you have applied the epoxy. The best way is to be conscious and being sure to maintain a consistent temperature of the room. Don’t forget - outgassing effects are resolvable and only temporary!
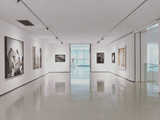
Adam Gibson
Jul 5, 2018
1 comment
Why Are There Bubbles in My Epoxy Flooring?
Previous post
How to install epoxy garage floors?
Next post
Spilled Epoxy Resin - What Should I Do Next?
1 comment
Can I just fill in the bubble clusters instead of doing the hole floor the seal it with clear coat?